Reduced drag and increased engine performance equal speed on the 2.5-mile Indianapolis Motor Speedway oval, and Honda Performance Development COO and vice president Steve Eriksen believes its Verizon IndyCar Series entries in the 99th Indianapolis 500 Mile Race will have all three with its superspeedway aerodynamic bodywork platform and 2.2-liter, twin-turbocharged V-6 engine.
Honda’s superspeedway aerodynamic bodywork package on the No. 29 TE Connectivity Andretti Autosport entry to be driven by Simona de Silvestro unveiled today at Indianapolis Motor Speedway features a range of options available to teams to utilize for qualifications and the 200-lap race. The platform was designed, developed and supplied by California-based Honda Performance Development, and the aero kit will make its public on-track debut May 3 during a Promoter Test at IMS. Chevrolet's superspeedway aero package also will be on track May 3.
Click it: Promoter Test details || Participant list
Practice opens May 11, with qualifications May 16-17 and the 99th Running of the Indianapolis 500 on May 24. Ryan Hunter-Reay, driving the No. 28 DHL Honda for Andretti Autosport, won the 2014 Indianapolis 500.
"We do expect faster speeds. You’ve seen it already on the road and street courses," Eriksen said.
The superspeedway package includes a variety of individual aerodynamic components fitted to the Honda-powered Dallara chassis but is markedly different from the road/street and short oval kit that has been utilized in the first four races of the Verizon IndyCar Series season. The front wing of the superspeedway kit contains fewer components to reduce drag and a rear wing element that Eriksen said is wide "like a glider." The rear wing main plane has "swan neck" supports that are carried over from Honda's sports car program, where HPD engineers learned that they helped with air flow over the rear wing. The rear wing main plane is unique to the Indianapolis 500, though an entry has the option to run the main plane to be used on the other three big ovals.
"One of the great things about IndyCar is that this aero kit has to operate over such a diverse range of circuits, it's unlike any other racing series, and it's a real challenge to make a kit that is going to work on every track well. But we welcomed it and have enjoyed doing it," Eriksen said. "The process really started with us looking at what has made us successful. The Indy 500 wins that we've had we look at and say, 'What did we do well and what could we do better in the future.' We wanted to build on that experience to build the best kit possible, and I think we've done that."
There will be visual differences between the Honda and Chevrolet superspeedway kits, within both manufacturers’ qualifying and race specs, and within their respective teams that likely will run different elements – even asymmetrical on the cars – during practice to fine-tune their cars.
“We’re excited to unveil our superspeedway aero kit, the newest element in this era of enhanced manufacturer competition in the Verizon IndyCar Series,” HPD president Art St. Cyr said. “Coupled to our proven Honda Indy V-6 engines, these aero kits are the products of thousands of hours of research, development and testing, as we seek to give our drivers and teams the tools they need to win the race that Honda holds as its most important goal each season: the Indianapolis 500.”
Both manufacturers, under INDYCAR regulations, designed components in “legality boxes” that complement the standard components of the rolling chassis. Areas open for development in these legality boxes include sidepods, engine cover, rear wheel guards, front and rear wing main planes and end plates, superspeedway front wing main plane, and the Indianapolis 500 rear wing main plane. Standard components for all cars include the underwing, road course front wing and rear wing main planes, nose, mirror housing and roll hoop fairing.
The road/street and short oval and superspeedway aero kits were developed by utilizing the latest in Computer-Aided Design and Computational Fluid Dynamics technology, then validated using Driver-In-Loop simulators. The process allowed the aerodynamic direction to be determined before full-size components were created.
Full-scale wind tunnel testing was used to confirm performance characteristics and develop aero maps to be used during manufacturer on-track testing from early October 2014 through mid-January 2015.
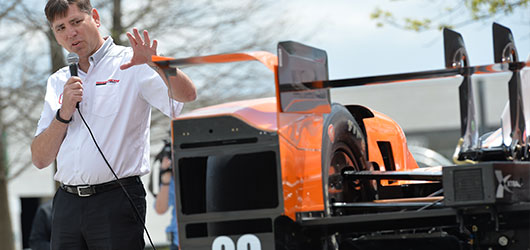
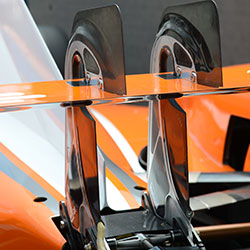
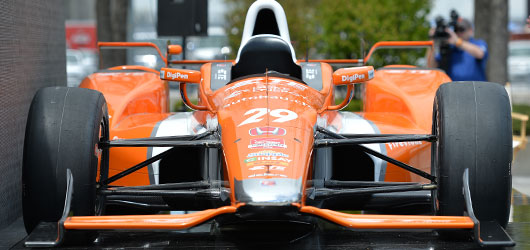